Principles and technologies
Additive manufacturing or 3D-printing, as it is more commonly known, is a collection of technologies that uses CAD (Computer Aided Design) and special machines to create physical objects. CAD software allows makers to create digital, three-dimensional, models of their ideas. Whereas 3D-printers provide the possibility to turn these models into real objects. There is a multitude of different types of technologies which can be used to power the machine we call a 3D-printer.
FDM (Fused Deposition Modelling) – This is the most widely used technology today. It powers the majority of machines used both in an industrial setting and for private use. The technology itself is based on the principle of melting a material, extrude it through a nozzle and draw two-dimensional layers. The nozzle is then moved vertically, and a new layer is printed on top of the last one. Stacking layers in this way eventually create a complete three-dimensional model. FDM models are typically made of polymers.
Vat Photopolymerization – Just as with FDM printing, this technology prints stacked layers but in a different way. Vat photopolymerization does not use the material extruding nozzle but instead uses photopolymer resin and a light source which emits light at a certain wavelength. Photopolymer resin is a liquid material that solidifies when exposed to the emitted light. By targeting specific areas of the resin, it is possible to create the layers which again forms a three-dimensional model.
PBF (Powder Bed Fusion) – PBF is somewhat similar to vat photopolymerization. It uses polymer or metal powder instead of resin and a high-power thermal source (like a high-power laser) instead of light. This thermal source is then targeted at areas of the powder which fuses together due to the heat. As with the other technologies, this process is repeated to form layers which together form the model.
Jetting – There are several forms of jetting, but for the sake of simplicity, just the core principle will be explained. Jetting uses a building material and a fusing mechanism. Building materials include metals, wax, rubber, ceramics and polymers. Consequently, the only demand for the fusing mechanism is that it causes the building material to fuse or harden. For example, if the build material is metal, then the fusing mechanism may be a high-power laser. While if the build material is photo-resin, it will be light. Now that seems very similar to the previously mentioned techniques. The main difference is that jetting emits building-material through a nozzle, almost like FDM. Then the dispensed material is cured or fused using similar methods to vat photopolymerization and PBF. In short, it can almost be considered as hybrid technology.
In the production
Currently, our technology of choice is FDM, as they are widely available, relatively low cost and very easy to operate. We have experimented with several different types of materials from standard PLA to engineering materials like PEEK. More importantly, we have capabilities to print in ESD-compliant materials, meaning we can print parts for usage in prototypes, and sometimes production.
We believe that the secret to deploy 3D printing in a manufacturing organization successfully is to include everyone. People who face challenges on a daily basis are more likely to find the right solution than engineers, who have no relation to the issue. Therefore, we have started teaching a wider group of our employees to design and print simple parts for themselves. Implementing it this way has accelerated the adoption of the technology, and our production environment is now full of 3D printed improvements.
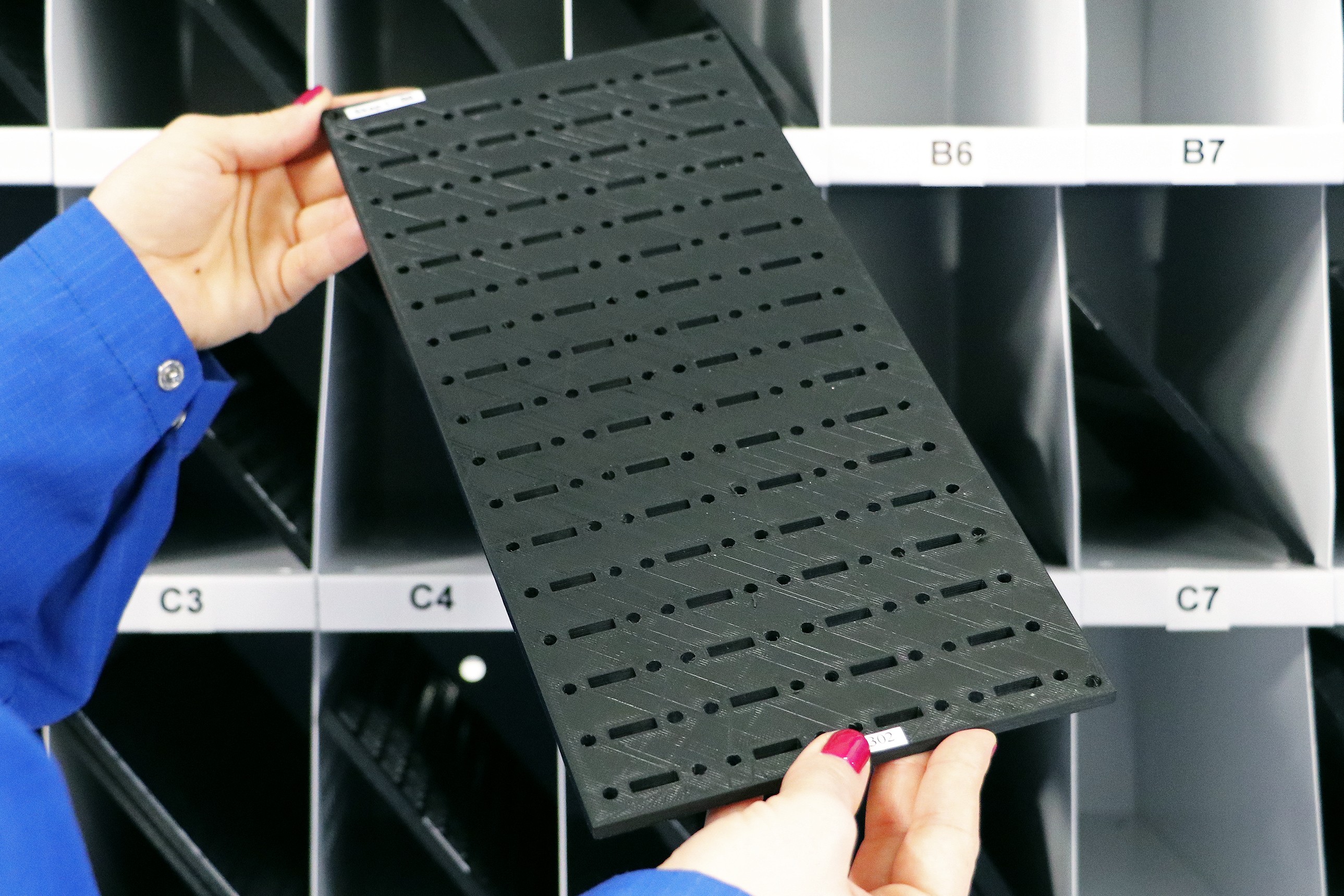
For the engineer
Of course, 3D printing is also of great use to our engineering department. Additive manufacturing allows us to do rapid prototyping, fast to market implementations and engineer our versions of machine parts. Such machine parts can be very expensive when bought from suppliers, and nearly free when we print them ourselves. And what happens when a part breaks? We print a new one!
Our printers are also used a lot for prototyping. We can test ideas for fixtures, tooling and other material before getting it produced by a machinist if it is necessary at all. Sometimes, we find that the 3D printed version works just fine. Other times, we need the part in a different material, if, for example, it is exposed to high temperatures or stresses. Note, that high is a relative term here, we have designed entire machines were some key parts that have been 3D printed. As with everything else, the design is crucial, it is possible to come a long way with “weak” plastic materials and creative engineers.
What does the future hold?
We are constantly looking for new possibilities within the field of additive manufacturing. Whether it be new materials, printing technologies or simply add-ons to our current printers. Now, the focus has moved to strong, high temperature, materials like PEEK or even metals. These are normally printed with machines that operate on technologies different from FDM. Therefore, we follow the development of them with curiosity and enthusiasm. Additionally, steps are being made on the topic expansions to FDM machines. We are, among other things talking about multi-material and colour support, slicing using stress analysis and stronger prints using composite materials. Stress analysis can be used to add extra material or material reinforcement strains to high-stress areas. The technique already available on the market is inserting carbon- or glass-fibres into the printed part, which makes more durable designs.
Summary
Bringing in 3D printers has opened new possibilities for us here at Kitron. We can make custom production equipment a lot faster and cheaper than earlier. And for engineers, it has never been easier to test out and verify new ideas for machines or customizations. 3D printers have changed the way we conduct our daily business, and we are looking forward to seeing what the future holds.